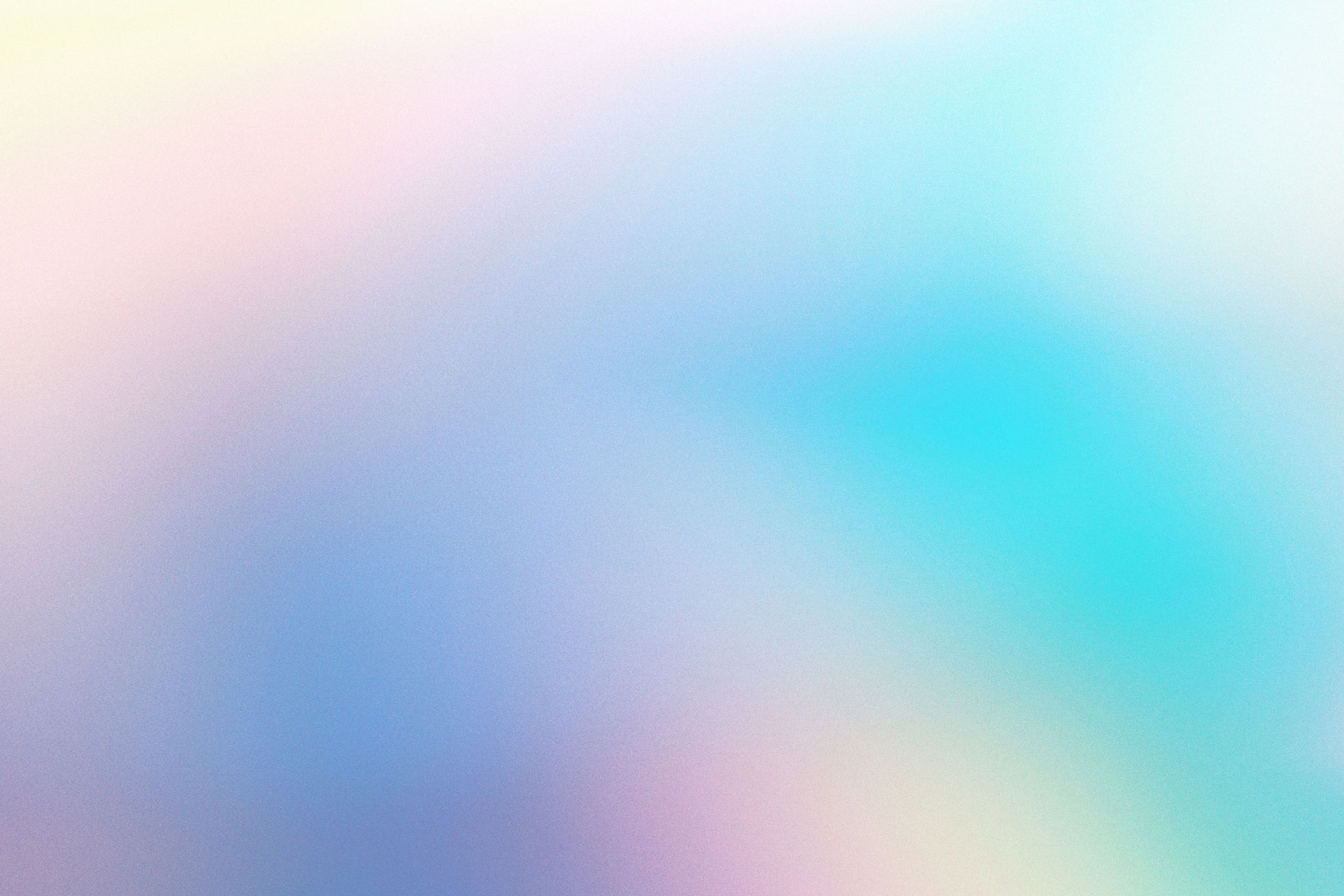
Star Rating
A star rating is a rating question that lets people rate a product or service with a number of stars. The number of stars can vary from 1 to 5 stars. A star rating question is a type of rating question that allows users to rank attributes on a scale represented with stars, instead of radio buttons or checkboxes.
Advantages of a Star Rating
-
Rating scales add a measure of data precision
-
They create standardization, allowing you to compare different people, topic, or products easily
-
They work as a general system; therefore, appraisals and assessments can be created for almost anything
-
They provide an opportunity for things to be graded fairly
-
Equality can be reached in a more successful manner than other systems that are more subjective.
We at JSNEPL, always try to fulfil the best of our work, quality, safety, employee, job competition period that is the completion of the job as fast as possible to achieve the best reputation in the minds of the company. From the date of the starting of the work with Tata Steel, we have always strived to fulfil Contract Safety Management System (CSMS).
Tool Box Meeting
A toolbox meeting, or toolbox talk, is a short periodical consultation at work, intended to make everybody aware of the different safety aspects and dangers at the worksites to increasing safety in the workplace. Toolbox meetings are mandatory in many countries to obtain and maintain certain certificates.
The secret to having successful toolbox talks is found in discussing the work situations that directly impact the personal safety and health of the employees.
We always keep in our mind that a severe accident can cost an employee his health and his career which we will not be able to bear for the rest of our life, while it may also cost the company millions in compensations.
Here, we organize toolbox meetings just to gain a hundred per cent confidence that there shall be no hazards while doing the work or post-work. For this, the senior employee, of our team conducts a meeting with its fellow employees in order to educate them about the hazards while doing the job so that there shall be no problem arising during the work period. We follow one policy that is “Work safe and go home”
Line Walk
A safety walk-around is when a line manager or supervisor observes work taking place, inspects the workplace, and discusses safety performance with staff based on their observations.
A walk-around is focused on the real experience of working every day. It’s designed to catch everyday unsafe practices that can compound over time to create serious risks for a whole group of employees. It’s also intended to help employees understand safety in real terms. By conducting a walk-around, a safety professional can point out unsafe practices when they occur in the real work environment, providing employees with safe alternatives and a means to understand why their practices are unsafe.
In this respect, safety walk-arounds are critical to employers because they make safety accessible to the workforce.
Mass Meeting
Safety meetings and safety talks are usually thought of as departmental or crew meetings. These frequent meetings, ranging from weekly to monthly depending upon the situation, allow the supervisor to review key safety topics, review any accidents incurred by members of the group, go over any unsafe practices observed, reaffirm the need for safe work practices, and to answer any questions that employees may have about equipment operation or other safety issues. Safety topics for such meetings and talks are often selected on the basis of the job given to us.
Topics for a safety meeting or safety talk is chosen on the basis of:
-
A review of the most recent accidents and near-misses at the facility.
-
Related corporate safety goals
-
Any particular subjects that need to be covered from a legal or insurance standpoint
-
Suggestions from employees, safety inspectors, contractor safety representatives, insurance representatives, or other knowledgeable observers
Important safety topics for meetings or talks include:
-
Safety around new equipment
-
Awareness of a new hazard
-
New regulations or policies
-
Safety orientation for new employees
Near Miss
While it’s natural to share close calls casually, reporting a near miss often goes against human nature. For one, reporting means taking time away from the task at hand. Two, it calls attention to everyone involved in an event that would have otherwise gone unnoticed. Many employees fear being blamed, shamed, or even punished for reporting.
Near misses are events that could have led to bodily harm and/or property loss.
A near miss report should lead to hazard resolution and preventative measures. However, if the event isn’t reported or addressed, a serious injury could easily result—possibly only hours later—from the same or similar circumstances. Here at the workplace, we always concentrate on the smallest of things to ensure that no fault is left behind from our side.
Covid-19 Protocol
When someone who has COVID-19 coughs or exhales they release droplets of infected fluid. Most of these droplets fall on nearby surfaces and objects - such as desks, tables or telephones. People could catch COVID-19 by touching contaminated surfaces or objects – and then touching their eyes, nose or mouth. If they are standing within one meter of a person with COVID-19 they can catch it by breathing in droplets coughed out or exhaled by them. In other words, COVID-19 spreads in a similar way to flu.
Ways which we follow to keep our self covid-19 proof
· Make sure that our workplaces are clean and hygienic
§ Surfaces (e.g., desks and tables) and objects (e.g., telephones, keyboards) need to be wiped with disinfectant regularly
· Promote regular and thorough hand-washing by employees, employers and customers.
· Put sanitizing hand rub dispensers in prominent places around the workplace. Make sure these dispensers are regularly refilled
· Promoting good respiratory hygiene in the workplace
· Ensuring that face masks (surgical mask) and / or paper tissues are available at our workplaces, for those who develop a runny nose or cough at work, along with closed bins for hygienically disposing of them
· We refrain from unnecessary travel both local and international.
· In case of unavoidable travel to locations reporting COVID-19,
§ We make sure all persons travelling are briefed by a qualified professional (e.g., staff health services, health care provider or local public health partner) and know what to do and who to contact if they feel ill while traveling.
§ We also avoid sending employees at higher risk of serious illness (e.g., older employees and those with medical conditions such as diabetes, heart and lung disease)
§ We encourage employees to wash their hands regularly and stay at least one meter away from people who are coughing or sneezing
§ We ensure that our employees comply with instructions from local authorities where they are traveling.
§ Employees who have returned should monitor themselves for symptoms for 14 days and then get back to work.
§ If they develop even a mild cough or low-grade fever (i.e., a temperature of 37.3 C or more) they are ordered to stay at home and self-isolate and report to the nearest designated health facility)
Employee Appreciation
Safety is also a marker of employee engagement. That’s because good safety reflects and encourages a positive “social exchange” in the company. Social exchange is your employees’ trust in and relationship with the company.
In this environment, employees tend to go above and beyond their job description because they feel it is the right thing to do for a peer, leadership or the organization. This willingness to follow a procedure, even when no one is watching or to step up and take on leadership at the moment is a sign of a very high functioning organization. Conversely, when employees feel no sense of connection to the organization or its leaders, we cannot expect safety activities to flourish.
The desired (safety) culture cannot just be imposed by rules or standards. It has to be continuously constructed, expressed and reaffirmed throughout the organization day to day routine. The more individuals of an organization (at all levels) build a desire for safety, the more safety becomes an effective shared value of that organization, and the more safety culture is enhanced.
Self Audit
As per the Contractor Safety Management System (CSMS) SOP, we check our own work and judge accordingly. A team has also been set up that visits the site quarterly and checks whether everything is going fine or not.